
Los resultados fueron contundentes: se identificaron oportunidades de reducir el consumo energético en un 12,6%, lo que se traduce en un ahorro anual de USD 40.961 y una disminución de 175 toneladas en emisiones de CO2. Además, gracias a un análisis más profundo del consumo en electricidad y gas, se logró detectar un ahorro en contratación de energía eléctrica por 25.000 USD/año y en gas por 20.700 USD/año.
Estrategias Implementadas para la Eficiencia Energética
El primer paso fue realizar una campaña de medición: Incluyó el diseño e instalación de medidores inteligentes en áreas clave de la planta, permitiendo un análisis detallado de los patrones de consumo a través de la plataforma Powermate. En total, se instalaron cinco medidores, un medidor en el tablero general y los demás en distintos procesos productivos.
Oportunidades de mejora vinculadas a la auditoría energética:
Gracias a los datos recopilados durante el relevamiento en planta y al análisis del comportamiento energético mediante el dispositivo Powermeter, se identificaron diversas oportunidades para optimizar el consumo de energía. Se priorizaron las acciones más simples y aquellas con costos bajos o nulos.
Se destacan las siguientes:
1. Relevamiento de energía
Durante el recorrido de la planta y analizando las forma de producción y como se manejaban en cuestiones energéticas, se realizaron recomendaciones para el uso de la energía, estableciendo criterios que ayuden a reducir los consumos de energía en la planta.
Esto se logró de manera más sencilla gracias a la utilización de los medidores Powermeter que permitieron detectar picos de potencia que no eran justificables y consumos de energía fuera de horarios laborales.

Heatmap de la potencia promedio en el suministro de la planta.
Ahorro estimado 26.105 kWh y 13.102 m3 representando 4.868 USD/año.
2. Optimización del uso de la iluminación
La implementación de sistemas de automatización para que se apaguen las luces cuando no se necesitan generaría una reducción del consumo a 9.720 kWh representando un ahorro de 788 USD/año.
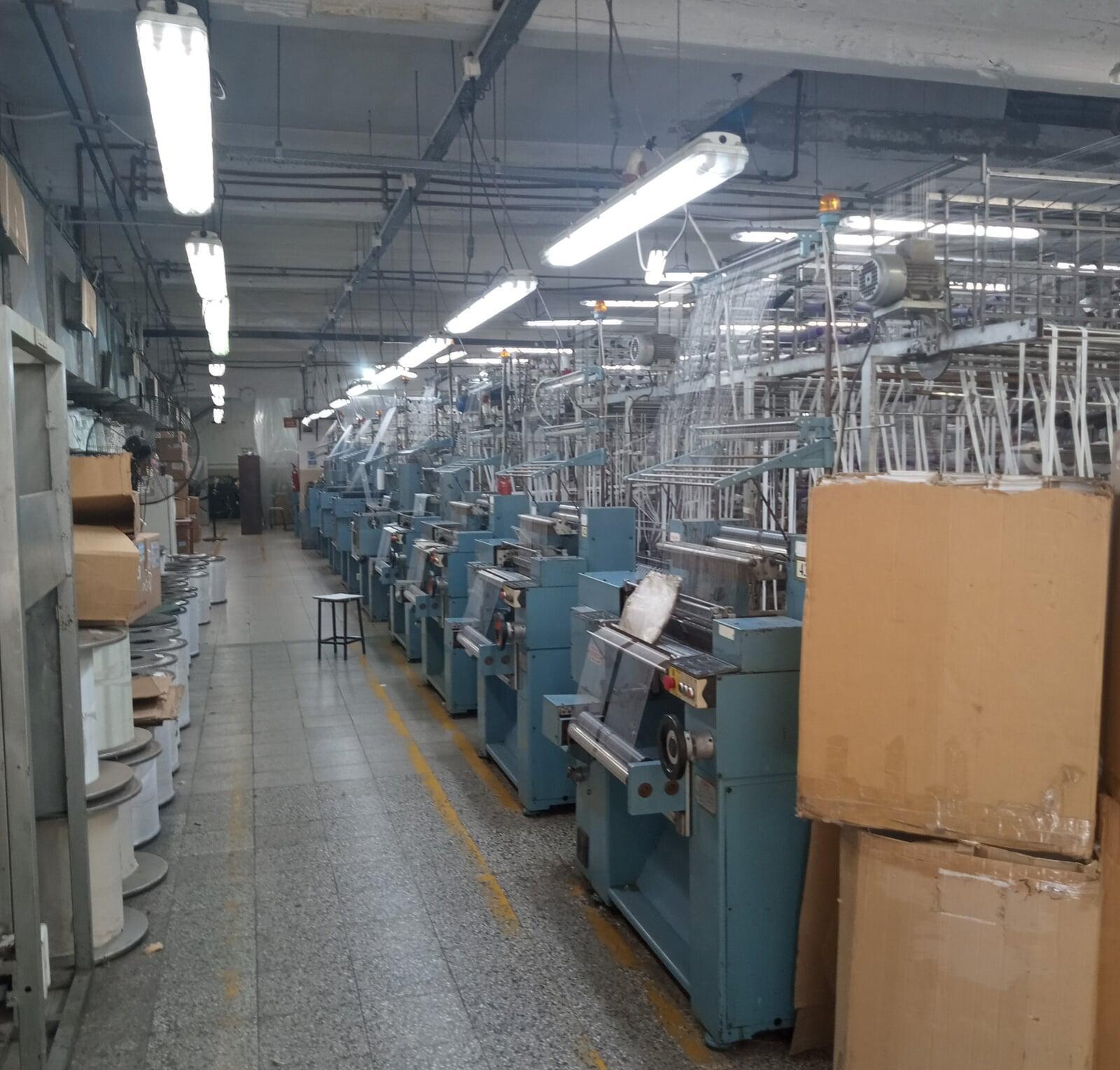
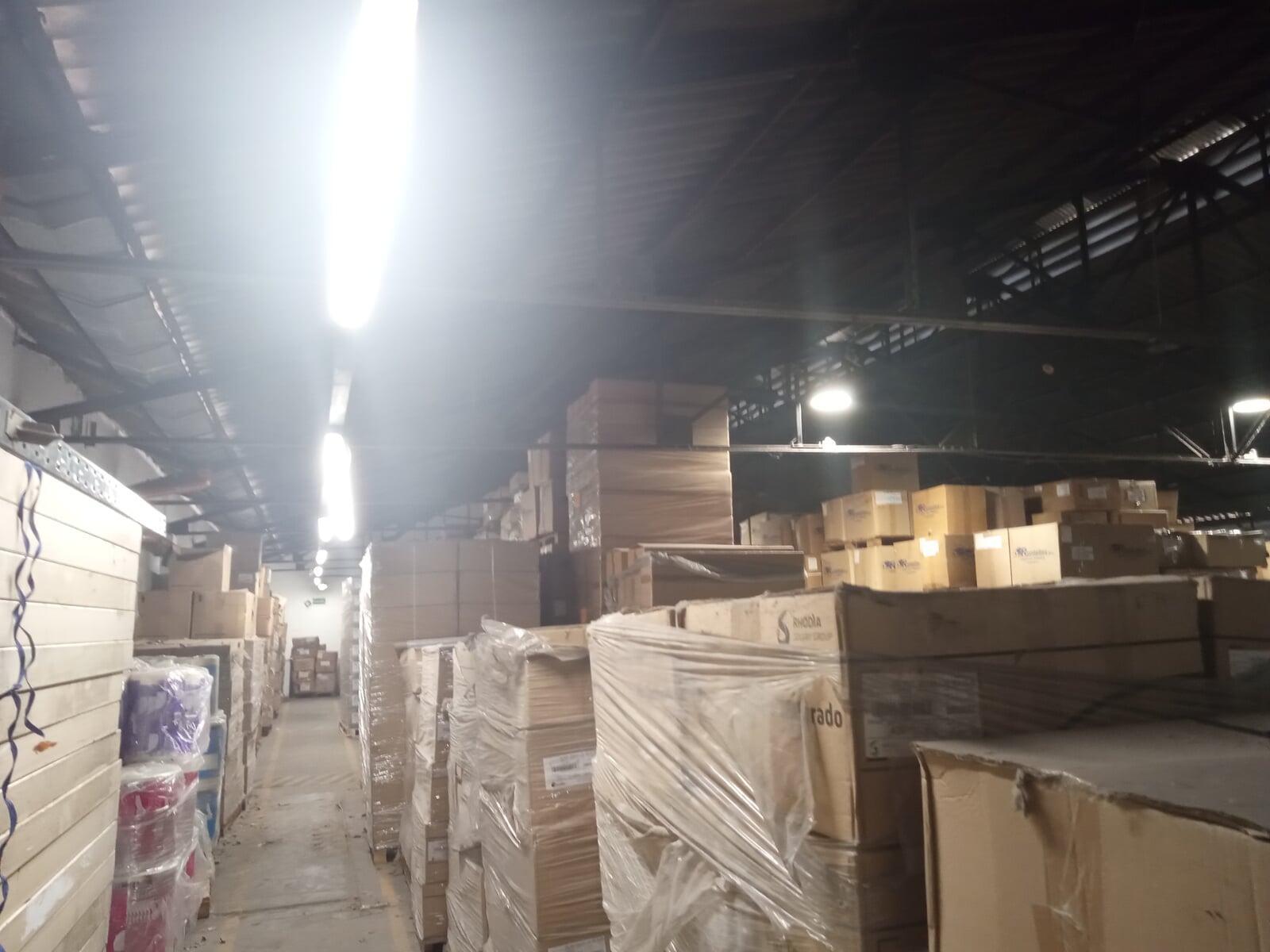
Iluminación de la fábrica
3. Distribución de vapor en procesos productivos
Se propuso la instalación de aislamiento térmico para reducir las pérdidas de calor en la caldera, cañerías y rodillos, logrando una reducción de 59.685 m³ y un ahorro estimado de 12.533 USD anuales. Adicionalmente, se evaluó la creación de una cámara aislante para los rodillos, minimizando la disipación de calor y optimizando la eficiencia térmica.
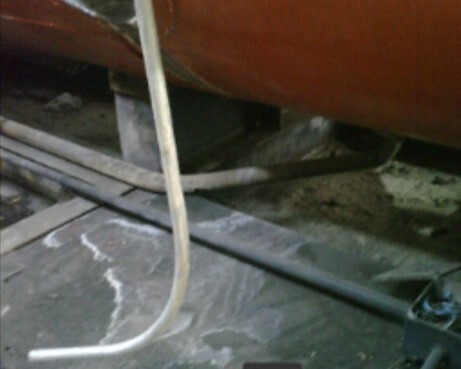
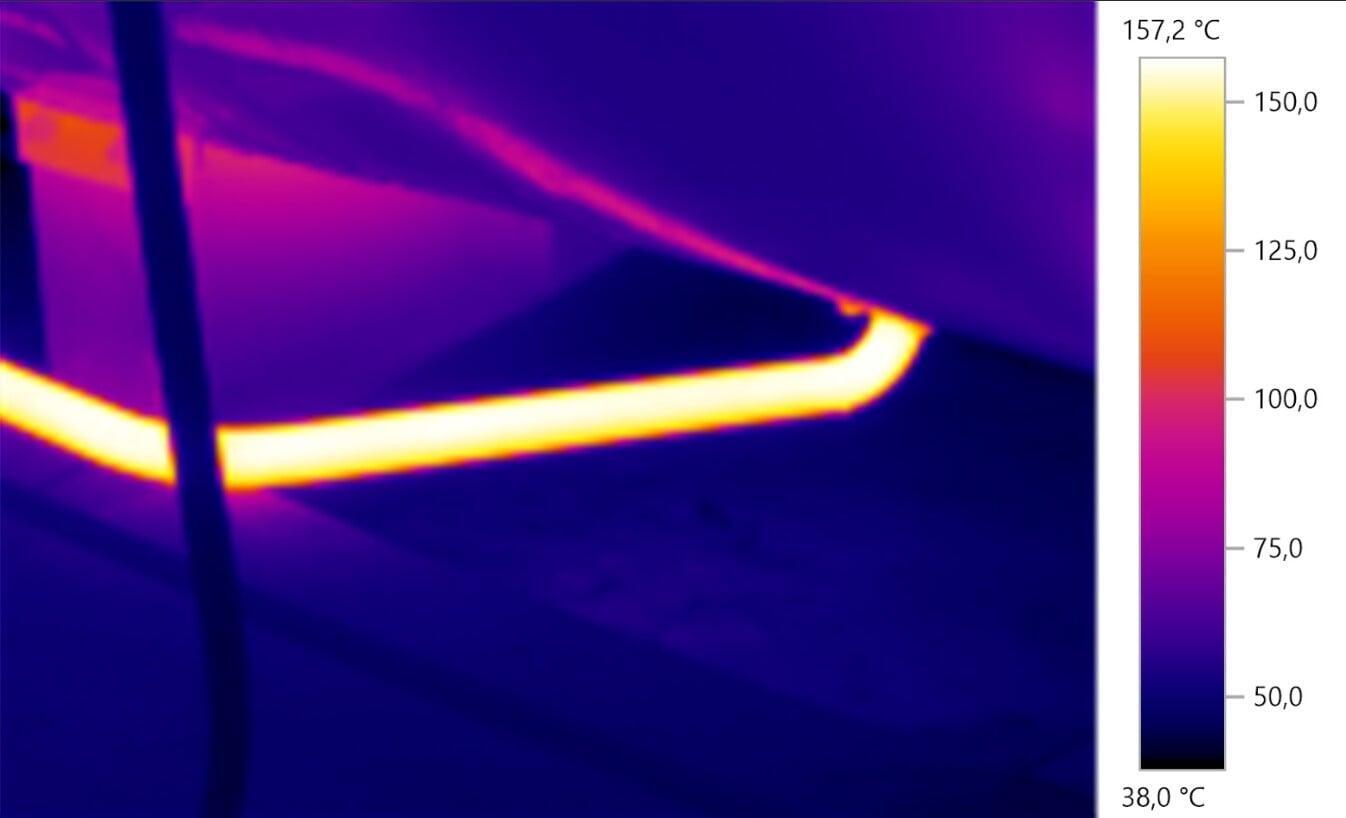
Pérdidas de calor en las cañerías por falta de aislamiento.
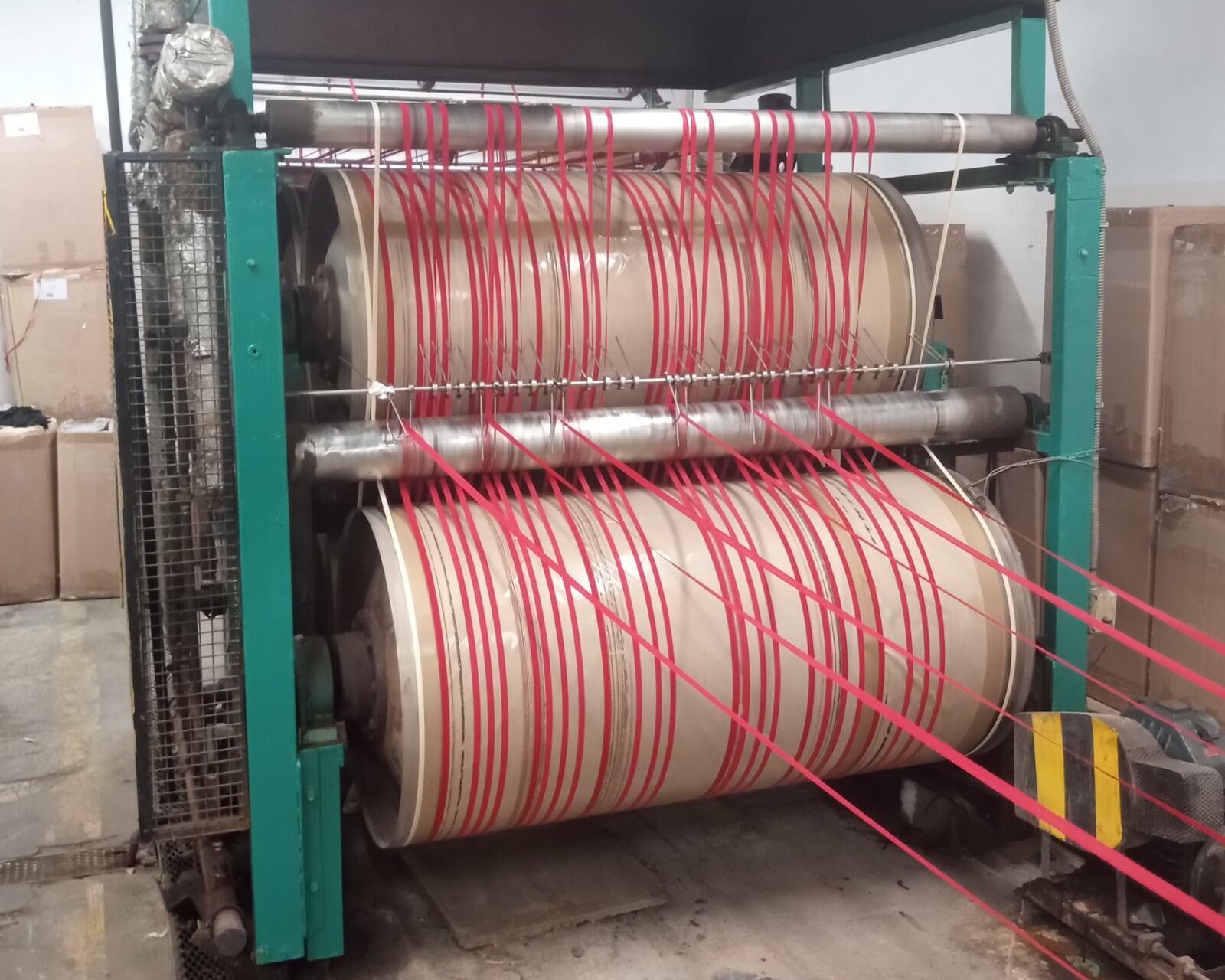
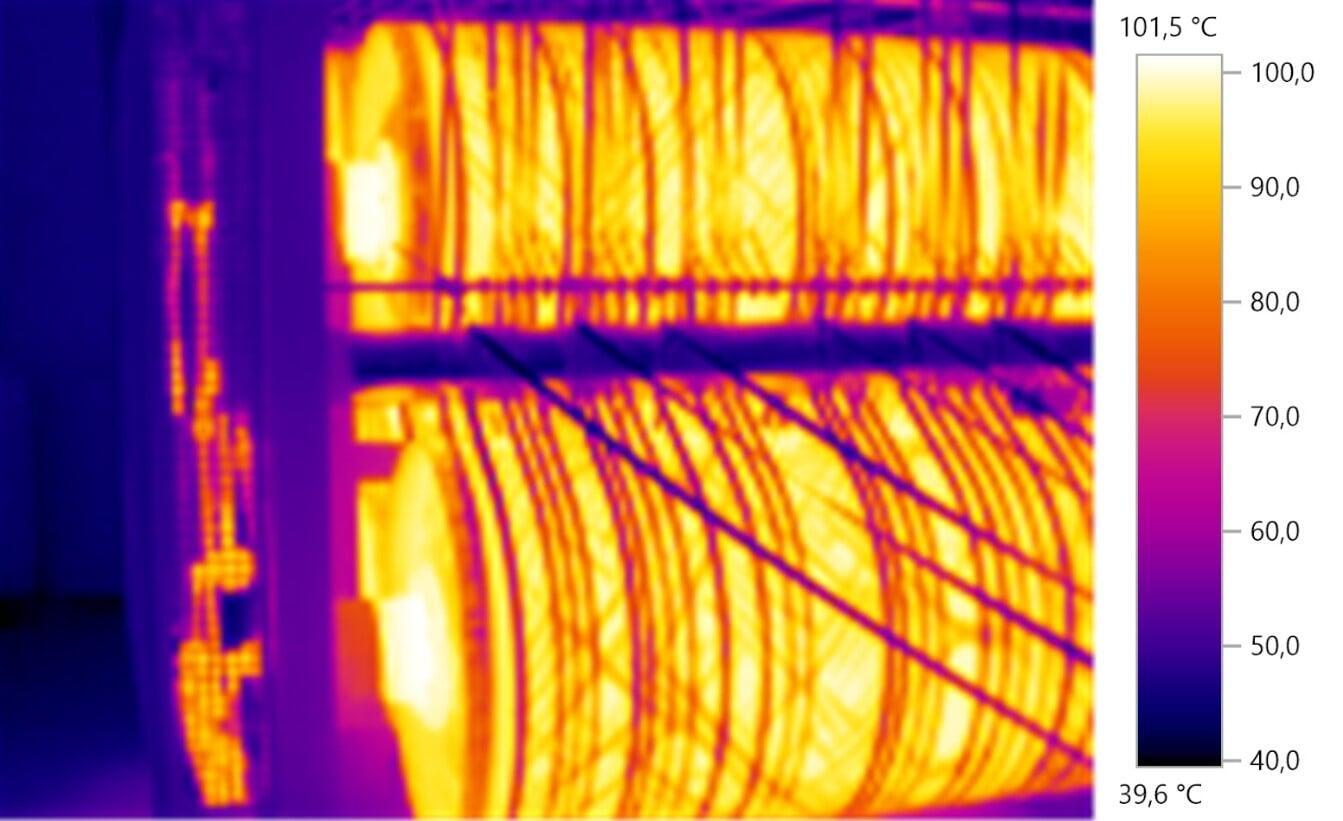
Los rodillos permanecen a una temperatura cercana a los 150°C.
4. Fugas de valor del circuito y en el tanque
Se propuso un sistema de detección y reparación de fugas que permitiría una reducción del consumo en 37.342 m³, generando un ahorro de 7.842 USD anuales.
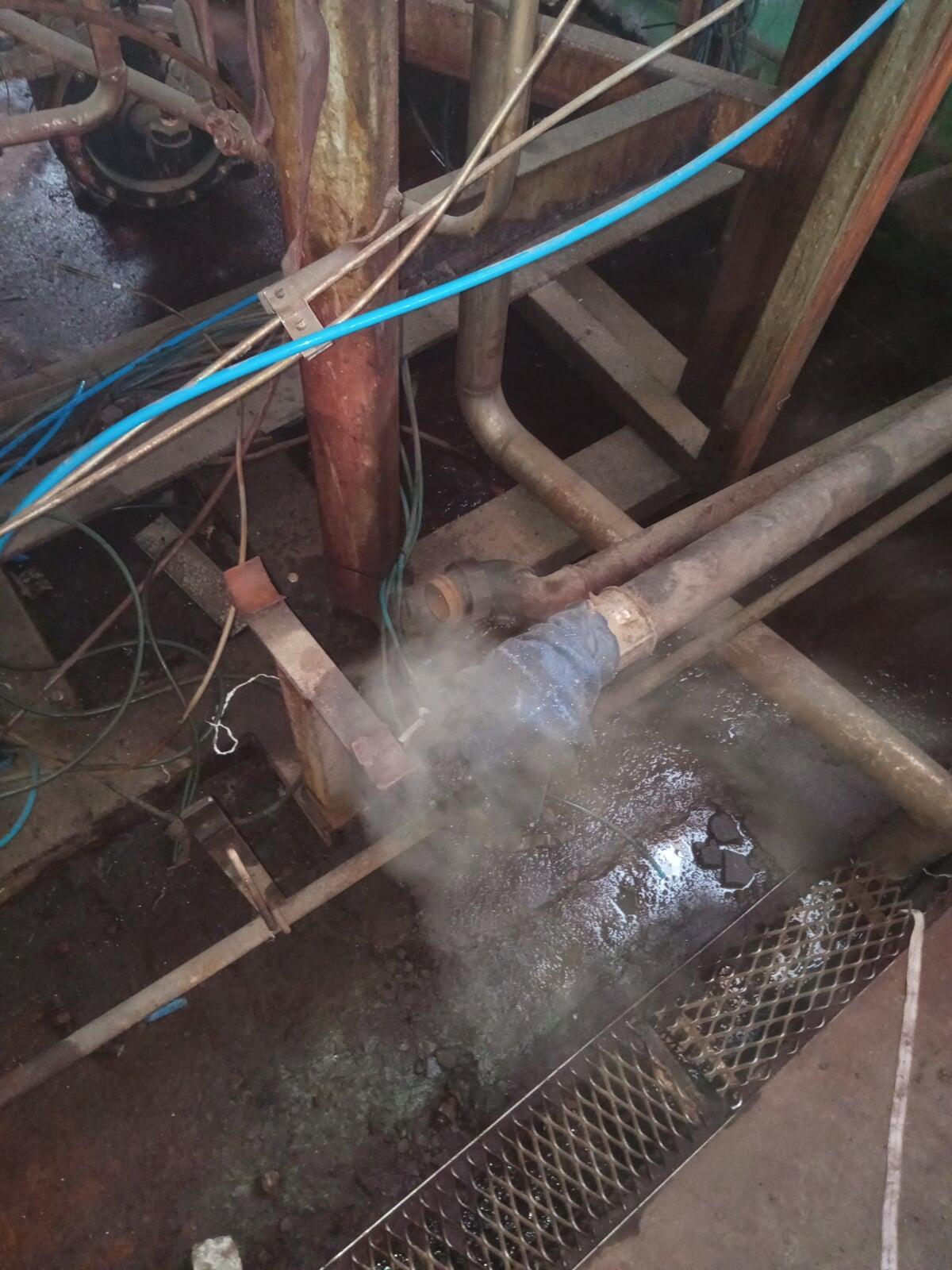
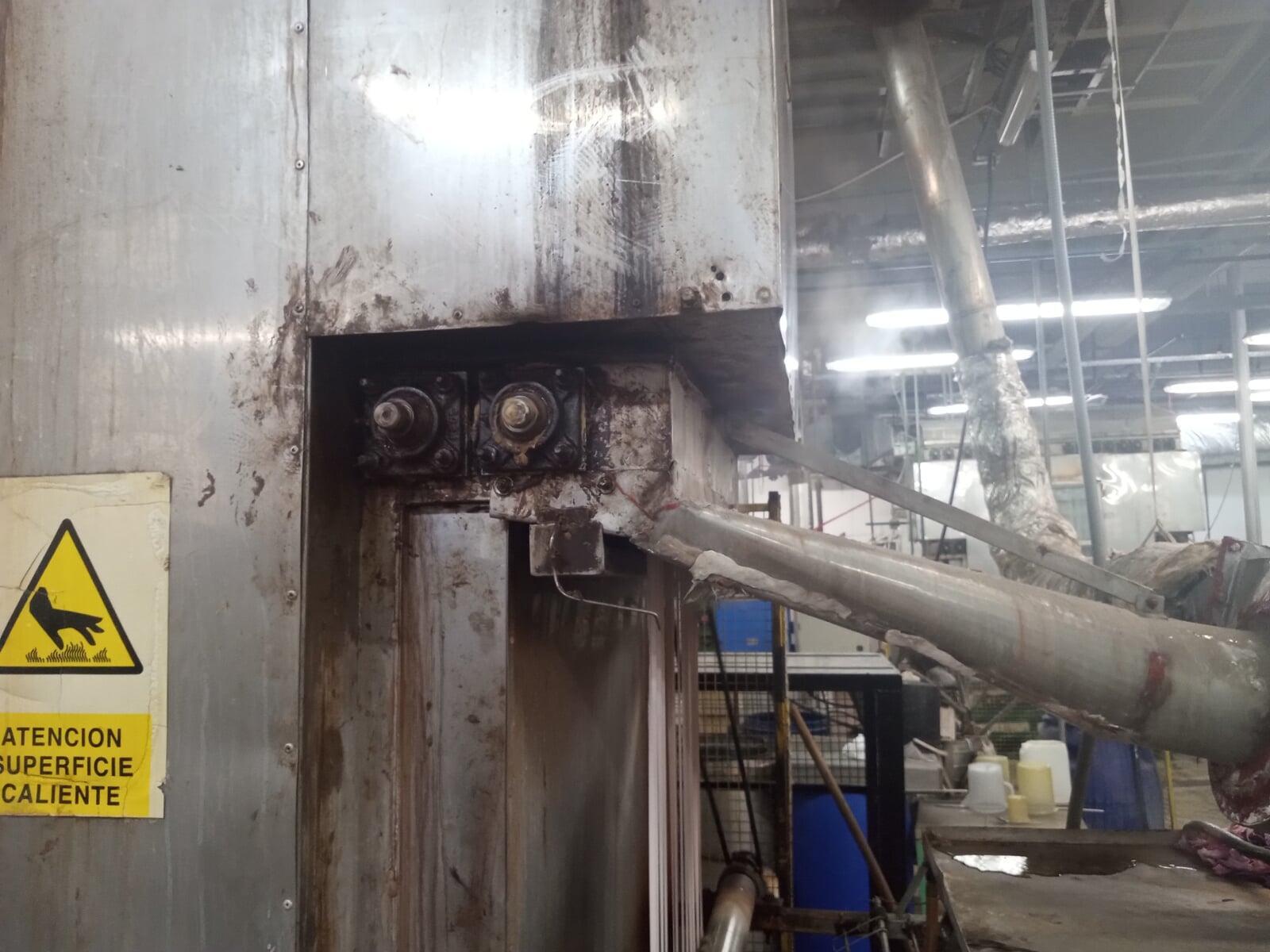
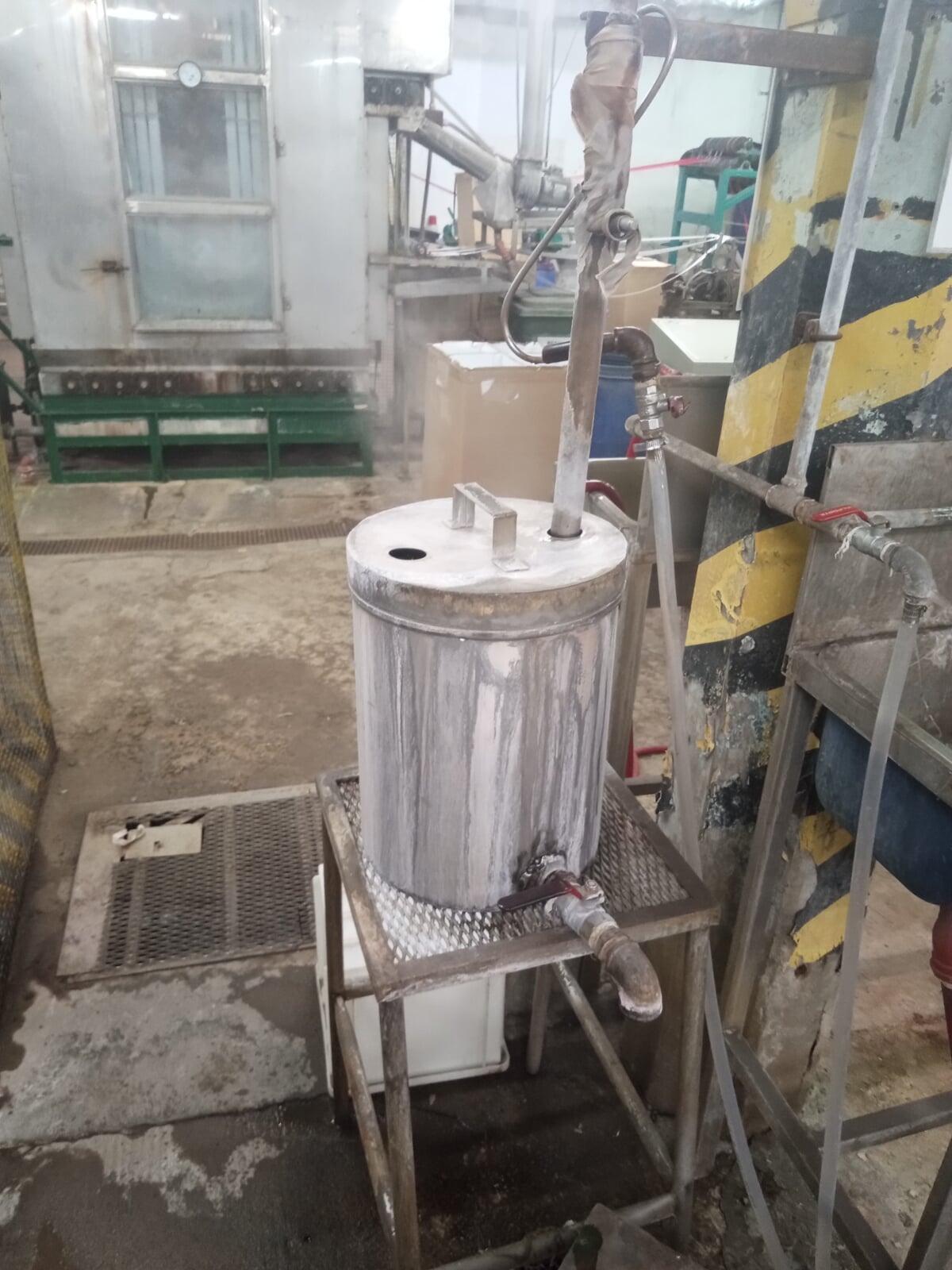
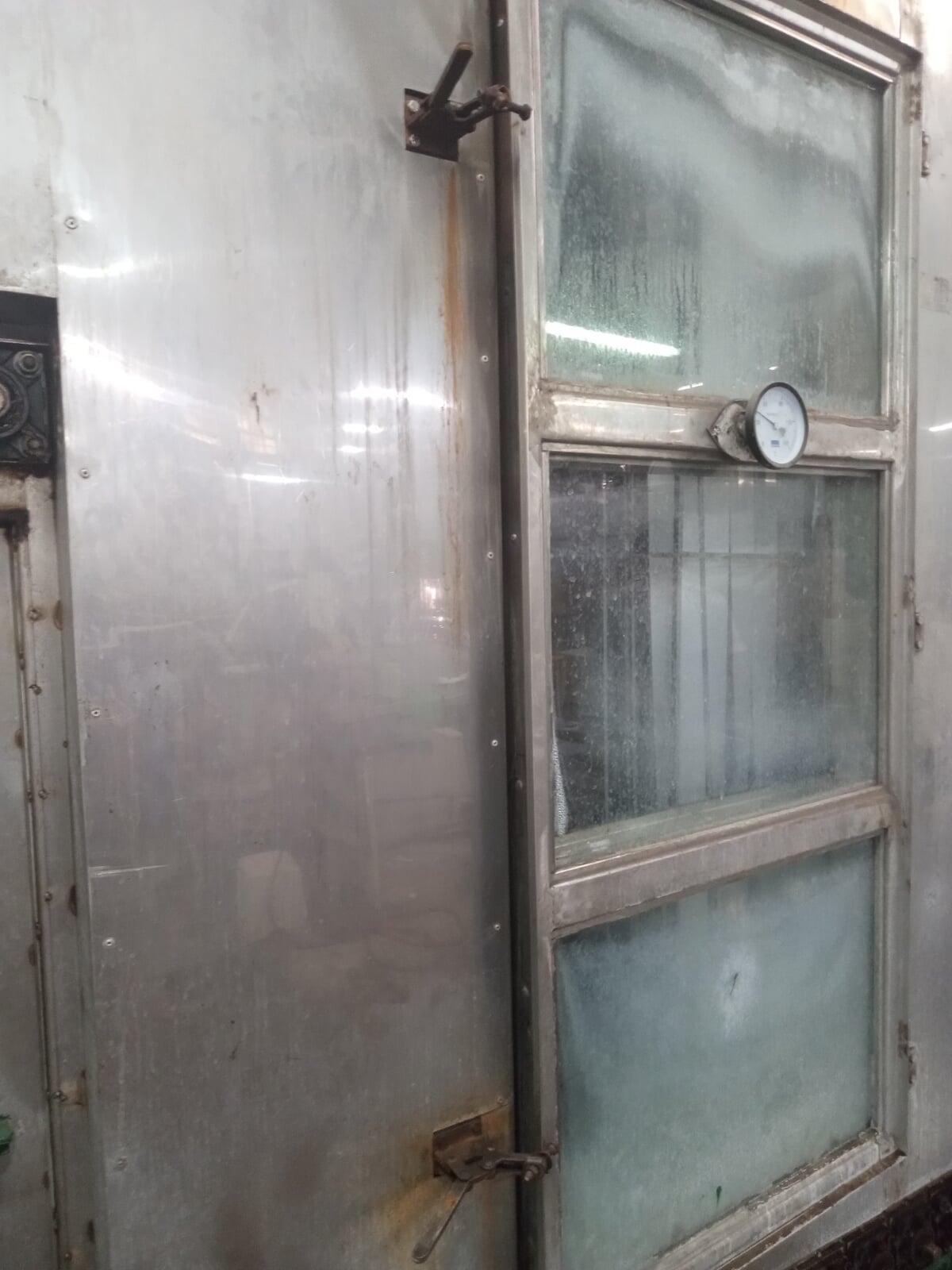
Pérdidas de vapor en el circuito o maquinaria.
5. Reparación de fugas de aire comprimido
Se detectaron fugas en el sistema de aire comprimido. La reparación de estas fugas permitiría reducir el consumo en 157.149 kWh, generando un ahorro de aproximadamente USD 12.744 al año.
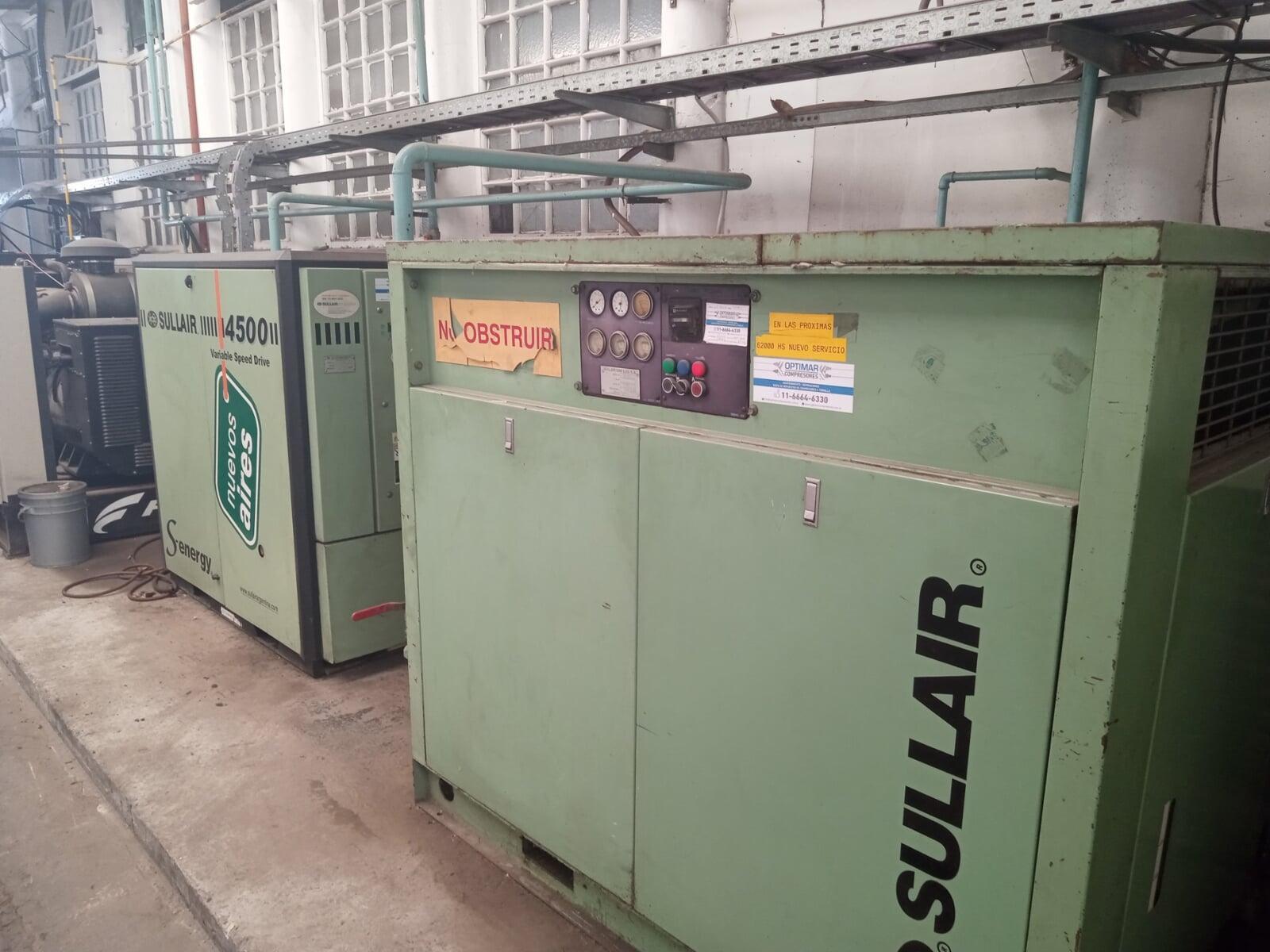
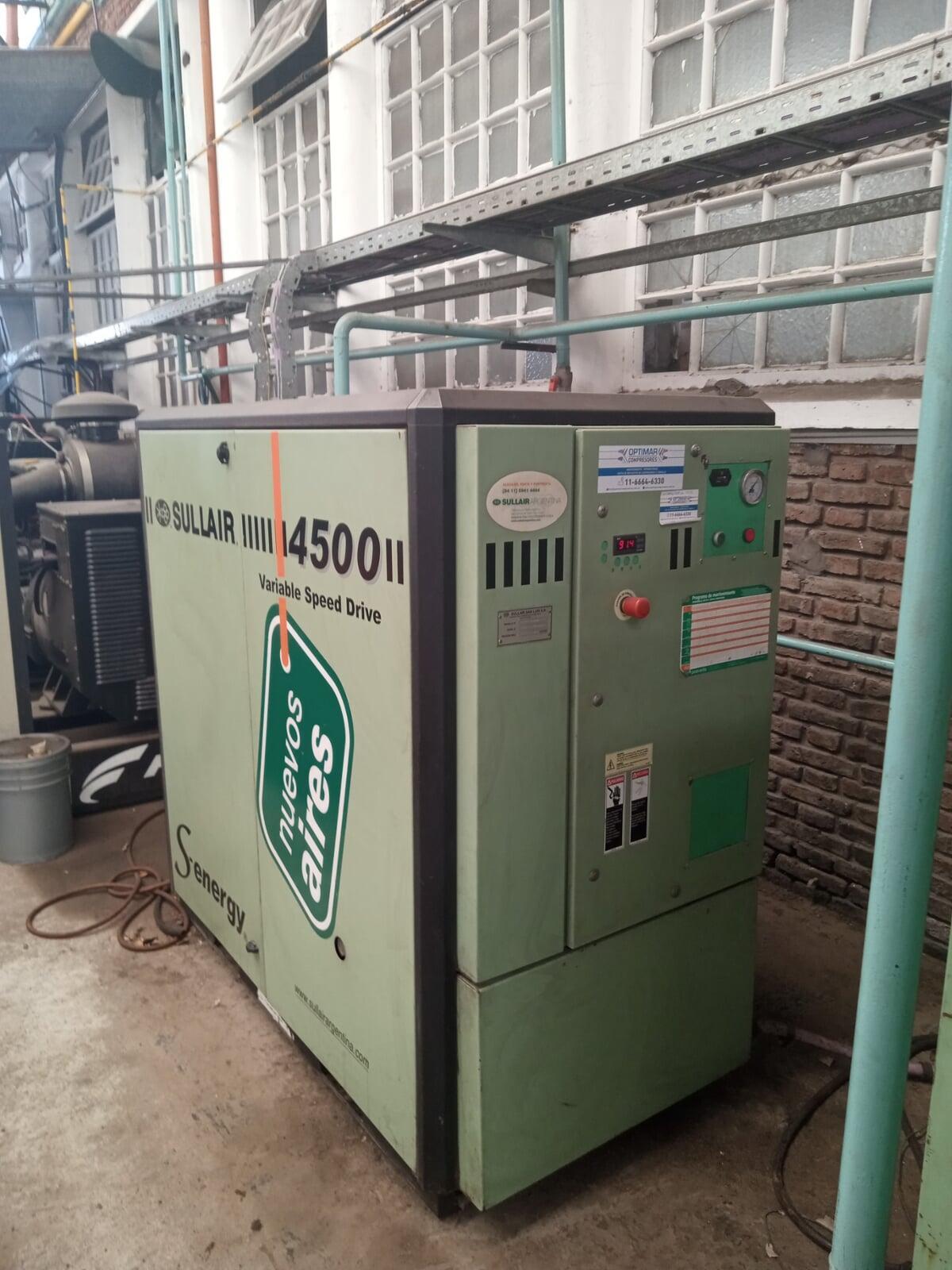
Compresores de la planta.
6. Envasado profiláctico
En este sector encontramos oportunidades en cómo se usa el horno de empaquetado (principal consumo del sector) y en el apagado de líneas cuando no están produciendo.

Izquierda: horno encendido, grupos de paquetes a la espera de pasar por el horno.
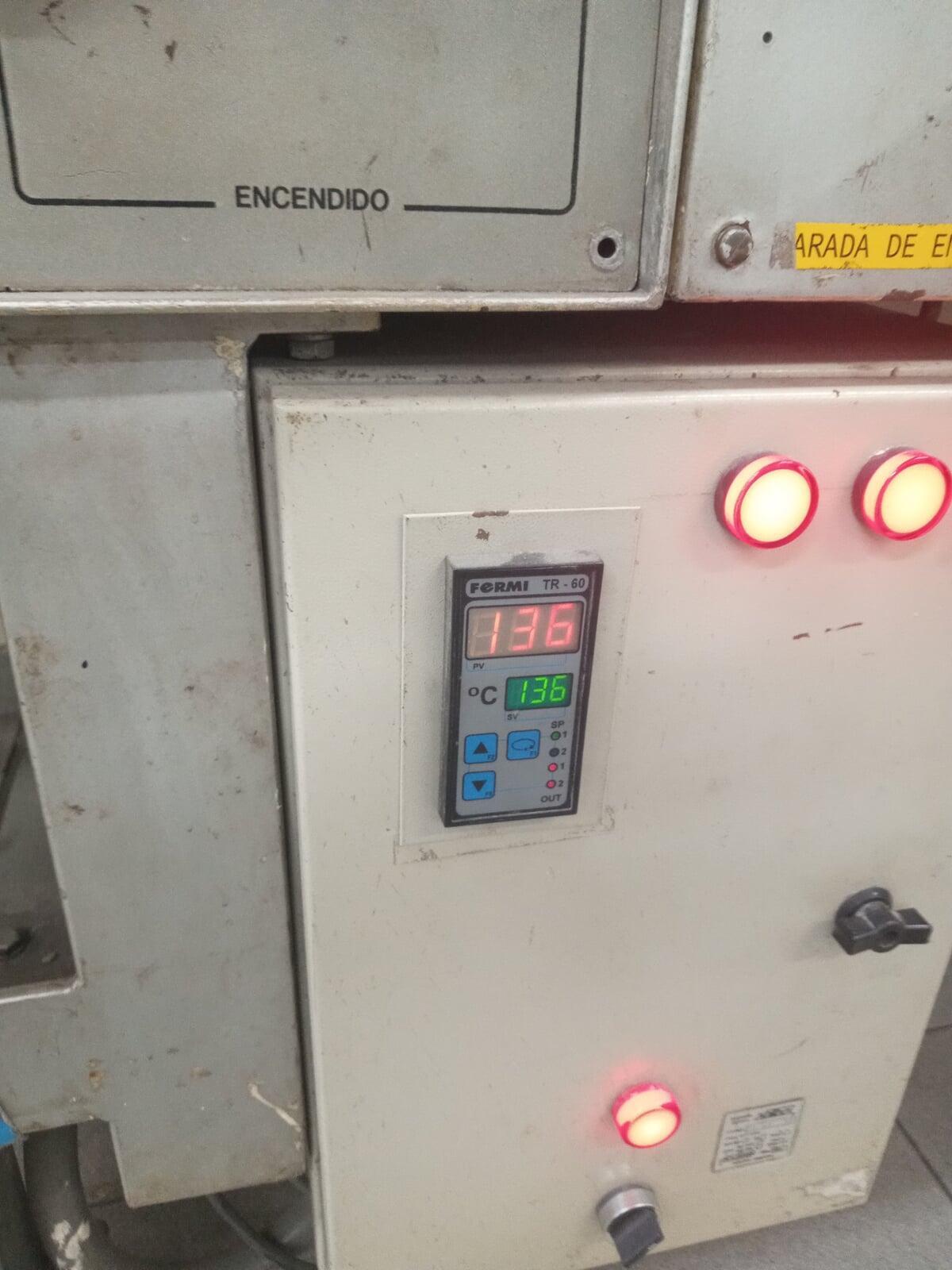
Derecha: temperatura de seteo.
Se logró un ahorro estimado de 56.957 kWh, lo que representa un beneficio económico anual aproximado de USD 2.186/año.
Optimización de Contratos Energéticos
Ahorro en gas
El costo del gas se descompone en tres grandes conceptos: transporte que representa el 51,8% de la factura, distribución con el 23,8% y los impuestos con el 24,4% restante.
Se analizó posibles oportunidades de mejora en el contrato, con el objetivo de optimizar los costos y obtener condiciones más favorables para futuros períodos. Finalmente se logró una mejora del contrato que implica una diferencia de 20.700 USD a lo largo de todo el año, generando aproximadamente un ahorro de un 20%.
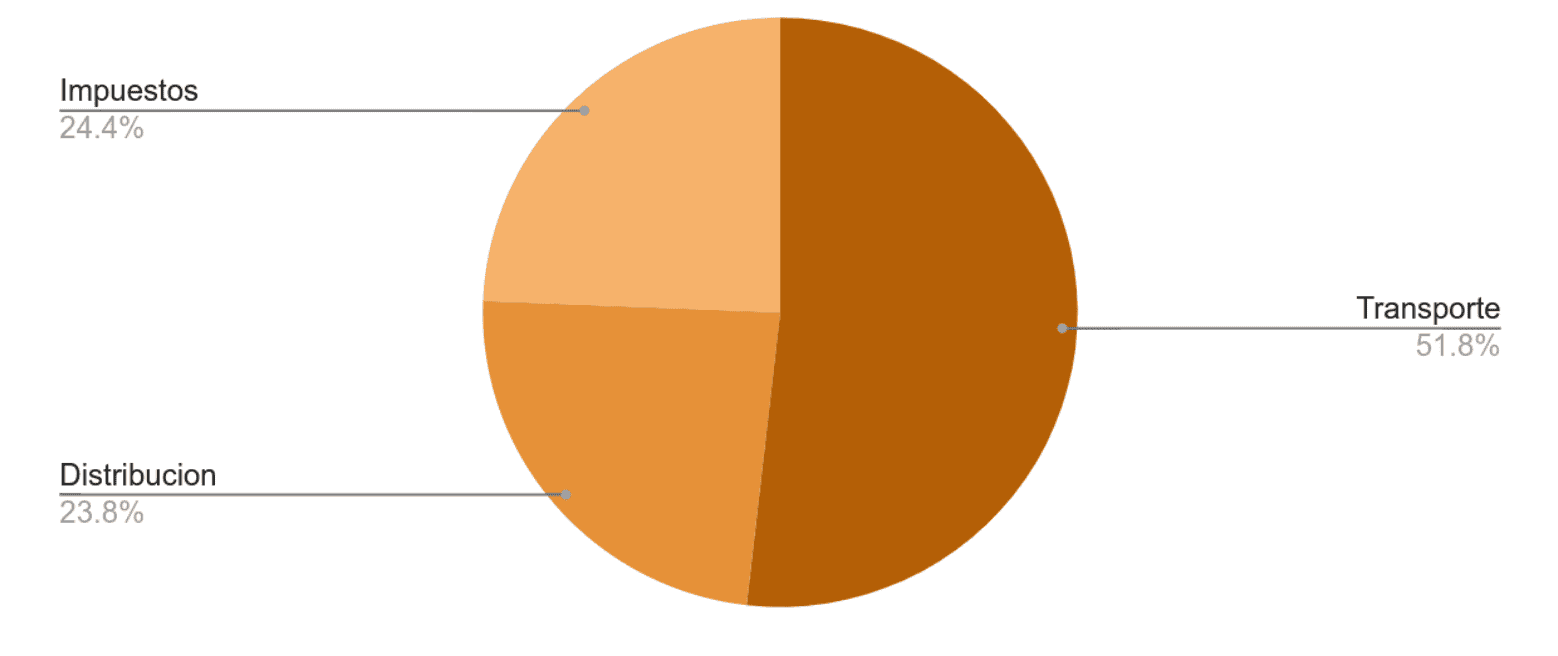
Ahorro en Electricidad
El suministro eléctrico de la planta pertenece a la distribuidora Edenor y corresponde a la categoría tarifaria T3-PEAJE. Estudiando la potencia adquirida de la planta detectamos una oportunidad de reducción de potencia para bajar los costos.
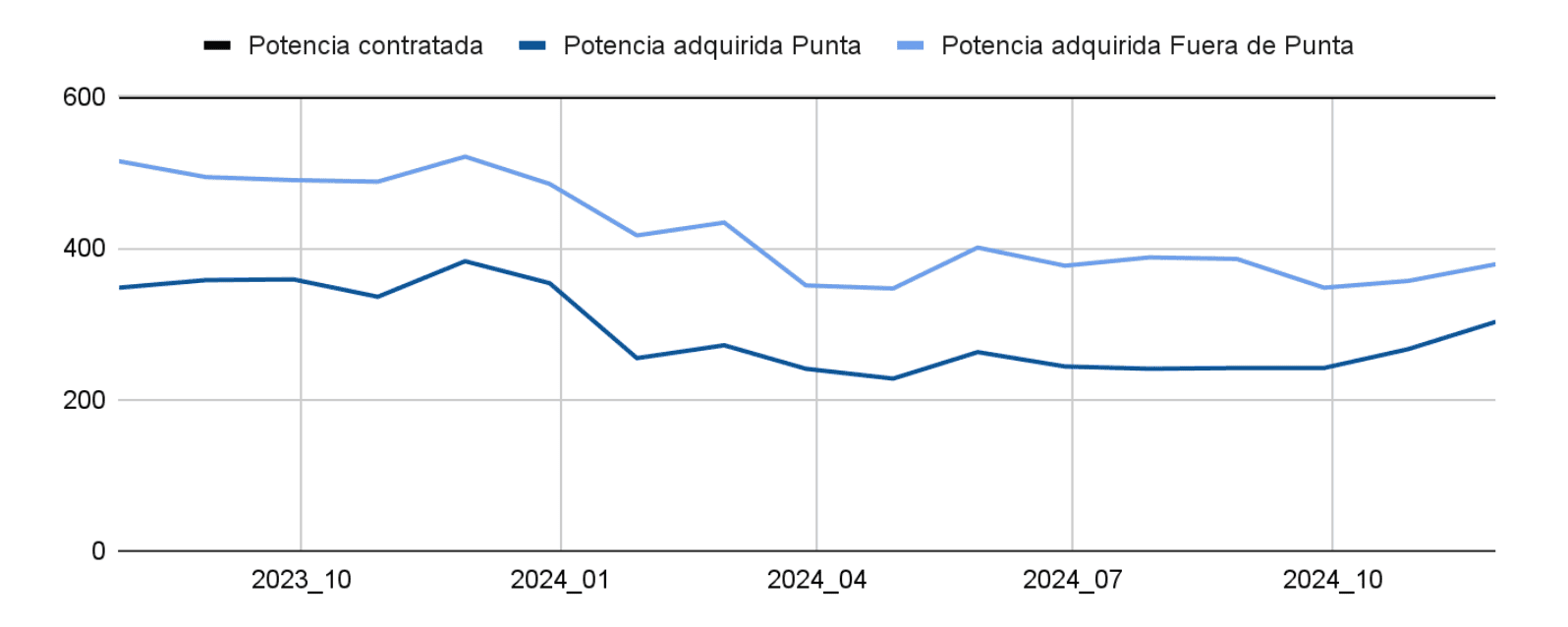
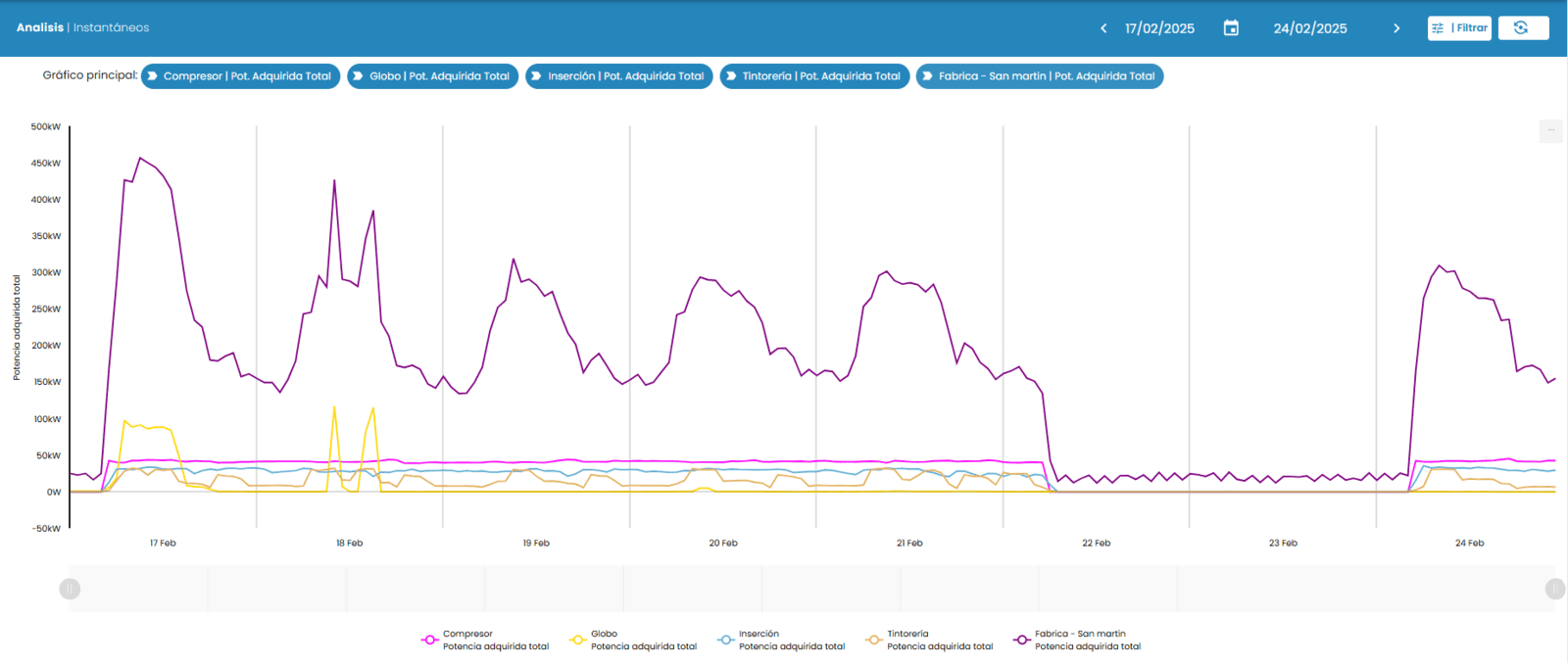
Demanda de potencia (en kW). La potencia contratada es 600 kW.
Gracias a los datos obtenidos por el medidor de Powermeter se realizo una reducción de potencia convenida pasando de 600 kW a 400 kW con un ahorro anual de 25.000 USD.
Resultados y beneficios obtenidos
Gracias a estas acciones, Kopelco pudo diseñar una estrategia con un Plan de Eficiencia Energética totalizando un ahorro energético de 220.000 kWh en electricidad y 110.129 m3 de gas al año aproximadamente 12,6% del consumo total de la planta. Esto se traduce en un ahorro económico de aproximadamente USD 40.961 anuales. La implementación de estas medidas, asimismo permitiría a la empresa reducir sus emisiones de CO2 en 175 toneladas al año, alineándose con su compromiso de sostenibilidad.
Se realizaron mejoras en los contratos de electricidad y gas, obteniendo condiciones más favorables en los precios de ambos servicios. Gracias a estas optimizaciones, se logró un ahorro anual de USD 20.500 en electricidad y USD 20.700 en gas, fortaleciendo la eficiencia energética y reduciendo costos operativos.
El caso de Kopelco evidencia que una auditoría energética meticulosa, combinada con la aplicación estratégica de mejoras, permite optimizar el rendimiento operativo, disminuir los costos y reducir sustancialmente el impacto ambiental en la industria.